When I first began working with industrial machinery, I quickly realized that no machine operates in isolation. Each piece of equipment is just one cog in a much larger system. Pipe coil wrapping machines, with their intricate designs and specialized functions, are no exception. These machines are essential for packaging coiled materials such as pipes, wires, and cables, ensuring they are protected during storage or transit. But as critical as they are, the question remains: can a pipe coil wrapping machine fit seamlessly into an existing production line?
At first glance, the integration process might seem straightforward. After all, it’s just about connecting one machine to another, right? But anyone who has worked in manufacturing knows it’s rarely that simple. Factors like compatibility, layout, automation, and communication protocols all play a role. A machine that isn’t properly integrated can disrupt workflows, create bottlenecks, and even lead to costly downtime. On the flip side, a well-integrated wrapping machine can enhance efficiency, reduce waste, and improve overall output.
The more I explored the complexities of integration, the more I realized that this isn’t just a technical challenge—it’s a strategic one. Whether you’re outfitting a new facility or upgrading an existing one, understanding how to integrate a pipe coil wrapping machine is critical to maximizing its potential. So, what does it take to make the integration seamless? Let’s dive deeper.
[claim] Integrating a pipe coil wrapping machine with existing equipment isn’t just possible—it’s essential for optimizing production and ensuring long-term operational success.
Table of Contents
1. What Are the Key Factors for Seamless Integration?

1.1 Compatibility with Existing Systems
When I first delved into the integration of pipe coil wrapping machines, compatibility stood out as the most critical factor. Without proper communication between machines, even the most advanced equipment can become a liability. For example, if your wrapping machine uses a modern Ethernet/IP interface but your existing conveyors rely on older Modbus protocols, the mismatch can disrupt the entire production line.
Beyond software communication, physical compatibility is equally important. A wrapping machine that isn’t dimensionally aligned with upstream or downstream equipment can create inefficiencies—such as coils not feeding properly into the wrapping zone. Customization at this stage often involves configuring the wrapping machine’s physical dimensions, software protocols, and workflow logic to match what’s already in place.
1.2 Efficiency Insights and Compatibility Data Table
To illustrate how integration impacts efficiency, here’s a breakdown of the key factors to consider:
Integration Factor | Impact on Workflow | Customization Options | Importance Level (1-5) |
---|---|---|---|
Communication Protocols | Enables seamless data exchange | Profinet, Modbus, Ethernet/IP compatibility | 5 |
Physical Dimensions | Ensures smooth material transfer | Adjustable conveyor height, modular connections | 4 |
Speed Synchronization | Matches wrapping speed to workflow | Variable drive motors, dynamic speed controls | 4 |
Power Supply Requirements | Prevents electrical mismatches | Voltage and amperage configurations | 3 |
Workflow Logic Integration | Synchronizes with upstream/downstream | Programmable logic controllers (PLCs) | 5 |
This table highlights the importance of addressing both technical and operational factors during the integration process. Overlooking even one of these aspects can lead to inefficiencies or downtime.
1.3 Layout Adjustments and Their Role in Integration
Physical layout plays a pivotal role in determining whether a pipe coil wrapping machine can be seamlessly integrated. The machine must align perfectly with upstream equipment, such as coil feeders, and downstream equipment, like unloading conveyors. A misalignment, even by a small margin, can cause jams, misfeeds, or damaged coils.
In one facility I worked with, the wrapping machine was installed on a raised platform to align with an existing conveyor system. This adjustment required customized supports and a slight modification to the machine’s base frame. While it added to the initial setup cost, the result was a smooth, uninterrupted workflow that eliminated the need for manual intervention.
1.4 Common Challenges and Solutions in Integration
Integration isn’t without its challenges. One of the most common issues is speed mismatches between the wrapping machine and other production line components. For example, if the upstream feeder delivers coils too quickly, the wrapping machine may struggle to keep up, leading to production delays.
The solution often lies in dynamic speed controls. By equipping the wrapping machine with variable frequency drives (VFDs), it can adjust its speed to match the pace of the production line automatically. Another challenge is ensuring that the wrapping machine’s software can “talk” to other machines. This may require middleware or custom programming to bridge compatibility gaps.
1.5 Fact or Fiction: Is Integration Always Feasible?
Fact: Most modern pipe coil wrapping machines are designed with integration in mind, offering adaptable dimensions, configurable software, and modular components.
Fiction: Integration is always straightforward. In reality, older equipment or highly specialized setups may require extensive customization—or even the replacement of legacy systems—to achieve seamless integration.
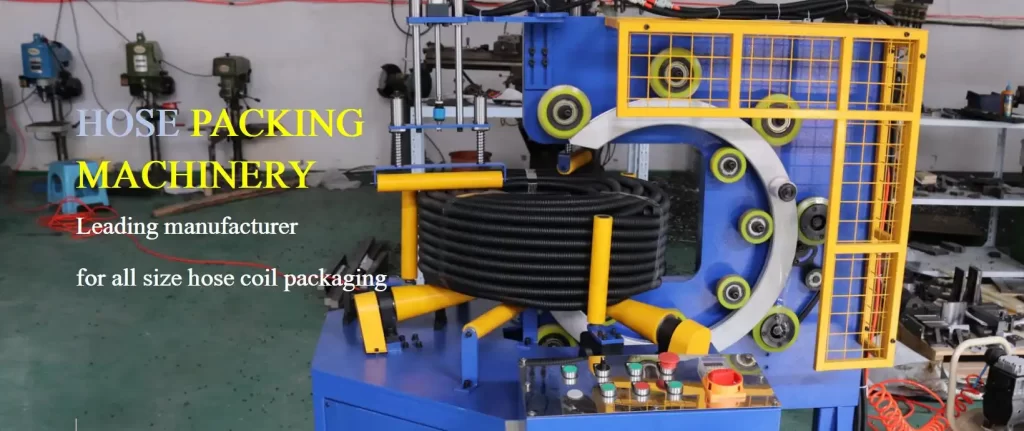
2. What Role Does Automation Play in Integration?
2.1 Enhancing Integration Through Automation
Automation is often the key to unlocking seamless integration between a pipe coil wrapping machine and existing equipment. In modern production lines, where speed and accuracy are paramount, manual adjustments can no longer keep up. Instead, automation bridges the gap by ensuring consistent, real-time synchronization between machines.
For instance, automated coil detection sensors can identify the dimensions and weight of incoming coils, allowing the wrapping machine to adjust wrapping tension and material feed automatically. Similarly, programmable logic controllers (PLCs) enable machines to communicate with one another, ensuring that the wrapping process starts as soon as the coil is delivered and stops when it exits. These features eliminate the guesswork and reduce human error, creating a more streamlined and efficient workflow.
But automation doesn’t stop at basic integration. It also allows for advanced customization. For example, wrapping patterns can be pre-programmed based on coil specifications. This means that whether you’re wrapping small PVC pipes or large steel coils, the machine automatically adjusts its operation to match the material's needs. Automation doesn’t just make integration possible—it makes it smarter.
2.2 Key Automation Features and Data Table
Here’s a table summarizing the critical automation features that enhance integration:
Automation Feature | Functionality | Benefits | Importance Level (1-5) |
---|---|---|---|
PLC Integration | Synchronizes machines via programmable logic | Real-time communication between systems | 5 |
Automatic Coil Detection | Identifies coil dimensions and weight automatically | Reduces manual adjustments | 4 |
Pre-Programmed Wrapping Modes | Customizable wrapping patterns for different materials | Ensures consistency and reduces setup time | 4 |
Dynamic Speed Adjustment | Matches wrapping speed to production pace | Prevents bottlenecks and maintains flow | 5 |
IoT Connectivity | Enables remote monitoring and control | Tracks performance and enables diagnostics | 3 |
These features showcase how automation not only simplifies the integration process but also enhances the overall functionality of the machine, ensuring it can adapt to varying operational demands.
2.3 Software and Programming Challenges
While automation can simplify integration, it also introduces challenges related to software and programming. One common issue is compatibility between communication protocols. For example, if your existing equipment uses Profinet but the wrapping machine operates on Ethernet/IP, a middleware solution or protocol converter may be required to establish communication.
Another challenge lies in programming the control systems. While PLCs are highly versatile, they require precise configuration to ensure that all machines on the production line work in harmony. Misconfigurations can lead to unexpected stoppages or inefficiencies. For instance, if the wrapping machine’s PLC isn’t programmed to account for varying coil sizes, it may apply too much tension to smaller coils, resulting in damaged products.
Investing in skilled technicians or working closely with the machine manufacturer to customize the software can mitigate these challenges. Additionally, choosing a wrapping machine with built-in software flexibility—such as open-source PLCs or user-friendly programming interfaces—can make the integration process far smoother.
2.4 Conclusion on Automation’s Role in Integration
Automation acts as the backbone of successful integration. By enabling real-time communication, dynamic adjustments, and advanced customization, it ensures that a pipe coil wrapping machine can operate seamlessly within an existing system. While there are challenges, such as protocol mismatches and programming complexities, these can often be addressed with the right expertise and planning.
The result is a production line that not only runs smoothly but also adapts to changing demands with minimal downtime. In industries where efficiency and precision are critical, automation is not just a convenience—it’s a necessity.
2.5 Fact or Fiction: Does Automation Guarantee Seamless Integration?
Fact: Automation significantly reduces manual intervention and ensures real-time synchronization, making integration much easier and more efficient.
Fiction: Automation guarantees perfect integration in all cases. While automation provides many advantages, successful integration still requires careful planning, programming, and customization to address compatibility and workflow-specific challenges.

3. How Can Integration Be Tailored for Industry-Specific Needs?
3.1 Adapting Machines to Industry-Specific Workflows
Every industry has unique requirements, and integrating a pipe coil wrapping machine into an existing workflow often requires tailoring it to meet these specific demands. For example, the construction industry often deals with large, heavy-duty steel pipes that require robust wrapping to protect against corrosion and damage during transport. In contrast, the electronics industry may handle smaller, delicate coils of wiring that need precise, lightweight wrapping for added protection.
Tailoring the integration process involves more than just physical adjustments. It often includes reconfiguring software to accommodate industry-specific wrapping patterns, material feeders, or even compliance standards. For instance, food-grade pipe manufacturers may need their machines to handle specific wrapping materials that meet hygiene regulations. These modifications ensure that the wrapping machine not only fits into the production line but also enhances its overall functionality.
3.2 Insights into Industry Challenges and Table of Solutions
Here’s a table showcasing common industry challenges and corresponding integration solutions:
Industry | Integration Challenges | Solutions |
---|---|---|
Construction | Heavy-duty pipes with large diameters | Reinforced turntables, extended wrapping heads |
Electronics | Delicate wiring coils requiring precision wrapping | Adjustable tension controls, fine wrapping modes |
Logistics | High variability in coil sizes | Multi-size compatibility, automatic detection |
Automotive | Corrosion prevention for metal pipes | VCI film compatibility, material feeders |
Food/Pharmaceutical | Compliance with hygiene standards | Food-grade wrapping materials, custom feeders |
This table highlights how different industries face unique challenges when integrating a wrapping machine and how specific solutions can overcome these obstacles.
3.3 Specialized Add-Ons for Custom Integration
Industry-specific integration often involves adding specialized components to the wrapping machine. For example, manufacturers working with sharp-edged steel coils may require reinforced tensioners and wrapping heads to prevent material tears. Similarly, industries that handle lightweight materials might prioritize integrating soft-start mechanisms to prevent sudden jerks during the wrapping process.
One interesting example I’ve encountered involved a logistics company that required their wrapping machine to handle multiple coil sizes without frequent manual adjustments. The solution? A dual-material feeder equipped with automatic size detection. This add-on allowed the machine to switch seamlessly between different wrapping materials and sizes, significantly reducing downtime.
3.4 Cost-Benefit Analysis of Industry-Specific Customizations
Customizing a pipe coil wrapping machine for industry-specific needs often comes with additional costs, but the long-term benefits usually outweigh the initial investment. For example, integrating a machine with VCI film compatibility for the automotive industry may cost an additional $5,000 to $10,000, but it can prevent up to $50,000 annually in losses due to rusted products.
Similarly, adding automation features like coil size detection and dynamic speed adjustment may increase upfront costs by 15-20%, but these features can boost productivity by 30-50%, leading to significant savings over time. Tailored solutions not only enhance performance but also ensure compliance with industry standards, further protecting the business from potential fines or recalls.
3.5 Fact or Fiction: Does Customization Always Increase Complexity?
Fact: Customization often requires additional planning, programming, and testing, which can increase the complexity of integration.
Fiction: Customization always makes systems harder to manage. In reality, well-implemented customizations simplify long-term operations by reducing manual intervention and improving workflow efficiency.
4. What Are the Long-Term Benefits of Seamless Integration?

4.1 Long-Term Productivity Gains Through Integration
When I first saw a well-integrated pipe coil wrapping machine in action, I realized how much it could transform a production line. The machine wasn’t just wrapping coils; it was part of a synchronized system that operated like a well-oiled machine. The upstream conveyor fed the coils at the perfect speed, the wrapping machine adjusted dynamically to each coil’s size, and the downstream conveyor whisked the wrapped product away without hesitation. This level of harmony doesn’t just improve productivity—it redefines it.
Seamless integration eliminates wasted time, reduces errors, and minimizes human intervention. For example, a fully integrated wrapping machine can process 20-30% more coils per hour compared to one that operates independently. Over a year, this translates to thousands of additional wrapped coils, reduced labor costs, and fewer bottlenecks. Integration isn’t just a technical achievement; it’s a strategic advantage that pays dividends over time.
4.2 Cost Savings and Efficiency Improvements
The financial benefits of integration don’t always appear immediately, which is why many businesses overlook them. However, when you examine the numbers, the long-term savings become undeniable. Consider this: a poorly integrated wrapping machine might cause frequent misfeeds, leading to 5-10 minutes of downtime per incident. If this happens 10 times a day, that’s nearly an hour of lost productivity daily—or 250 hours annually for a single shift operation.
Now compare that to a seamless integration. With proper speed synchronization and automated adjustments, these issues are virtually eliminated. Additionally, integrated systems reduce the need for manual intervention, cutting labor costs by up to 30%. Here’s a table that breaks down the potential cost savings:
Benefit | Annual Savings | Explanation |
---|---|---|
Reduced Downtime | $10,000 - $15,000 | Fewer disruptions due to misfeeds or stoppages |
Lower Labor Costs | $20,000 - $30,000 | Automation reduces manual handling requirements |
Improved Material Efficiency | $5,000 - $10,000 | Precise wrapping minimizes material waste |
Increased Throughput | $25,000 - $50,000 | Higher output translates to more sales revenue |
As this data shows, the efficiency improvements and cost savings from seamless integration make it a worthwhile investment, especially for high-volume operations.
4.3 Maintenance and Its Role in Sustaining Integration Success
One aspect of integration that’s often overlooked is maintenance. Even the best-integrated system can lose its efficiency if not properly maintained. For instance, if the wrapping machine’s sensors become misaligned, it could fail to detect incoming coils accurately, disrupting the entire workflow. Similarly, wear and tear on conveyors or rollers could lead to physical misalignments, causing jams or delays.
To sustain long-term integration success, regular maintenance protocols are essential. This includes routine inspections, software updates, and alignment checks. Many modern wrapping machines come equipped with IoT connectivity, allowing operators to monitor performance metrics and receive alerts for maintenance needs in real-time. By addressing issues proactively, businesses can avoid costly downtime and ensure that their integrated systems continue to operate at peak efficiency.
4.4 ROI Analysis of Well-Integrated Systems
For businesses hesitant about the upfront costs of integration, it’s worth examining the return on investment (ROI). A well-integrated pipe coil wrapping machine typically pays for itself within 12-18 months, thanks to increased productivity and reduced operational costs. Over a five-year period, the ROI can be as high as 300-400%, depending on the scale of the operation.
Here’s a closer look at the five-year financial impact of integration:
Category | Value Over 5 Years | Explanation |
---|---|---|
Additional Revenue | $125,000 - $200,000 | Increased throughput leads to more sales |
Labor Cost Reductions | $100,000 - $150,000 | Automation reduces manual workload |
Material Waste Savings | $25,000 - $50,000 | Precise wrapping reduces excess material use |
Maintenance Cost Reduction | $10,000 - $20,000 | Proactive maintenance prevents costly repairs |
These numbers show that while the upfront costs of integration may be significant, the long-term financial benefits far outweigh them. Businesses that invest in integration aren’t just saving money—they’re setting themselves up for sustained growth and success.
Conclusion

[claim] Seamless integration of a pipe coil wrapping machine with existing equipment is more than a technical feat—it’s a strategic investment in the future of your business. By reducing downtime, improving efficiency, and unlocking long-term cost savings, integration transforms your production line into a cohesive, high-performing system. With the right planning, automation, and maintenance, this investment will continue to generate value for years to come.