In fast-paced industrial environments, operational efficiency is paramount. Any delays or inefficiencies in the packaging process can disrupt supply chains, increase costs, and negatively impact customer satisfaction. Automated coil wrapping machines have emerged as a critical solution for businesses looking to streamline their workflows. These machines not only optimize the packaging process but also reduce bottlenecks, improve product consistency, and lower labor dependency.
The beauty of automation lies in its ability to handle repetitive tasks with speed and precision. By replacing manual wrapping methods with automated systems, businesses can significantly reduce downtime, eliminate human error, and enhance overall productivity.
When every second counts, an automated coil wrapping machine acts as a game-changer. It helps manufacturers meet tight deadlines, reduce material waste, and maintain consistent packaging quality—even at high production volumes.
[claim] Automated coil wrapping machines optimize workflow by increasing speed, improving consistency, and minimizing human intervention, thereby reducing operational delays and enhancing efficiency.
Table of Contents
1. Why Is Operational Efficiency Crucial in Packaging?

1.1 The Impact of Packaging Bottlenecks
Packaging is the final step before products leave the facility, making it a critical stage in the production process. Bottlenecks in this phase can disrupt the entire workflow, delaying shipments and creating backlogs in production. For industries dealing with steel coils or other heavy materials, manual wrapping processes can be slow and error-prone, leading to inefficiencies.
For example, if a packaging team can only wrap 10 coils per hour manually, but the production line outputs 20 coils per hour, the backlog quickly grows. This delay not only affects delivery schedules but also increases labor costs as workers attempt to catch up. Inefficient packaging systems can also lead to damaged products, further compounding the problem with returns and customer dissatisfaction.
1.2 Common Challenges in Manual Coil Wrapping (With Table)
Manual coil wrapping presents several challenges that hinder operational efficiency. Here’s a comparison of these challenges and how automation addresses them:
Challenge | Manual Wrapping | Automated Wrapping |
---|---|---|
Speed | Slow and labor-intensive | Fast and efficient |
Consistency | Inconsistent wrapping tension | Uniform and precise wrapping |
Labor Dependency | Requires multiple operators | Minimal operator involvement |
Material Waste | High due to uneven application | Optimized usage, minimal waste |
Risk of Damage | Higher due to uneven wrapping | Secure packaging ensures protection |
As shown in the table, automation eliminates many of the inefficiencies of manual wrapping, making it a vital tool for businesses looking to optimize their operations.
1.3 How Automation Drives Productivity in Packaging
Automation transforms the packaging process by introducing speed, precision, and reliability. Automated coil wrapping machines can handle repetitive tasks without fatigue, allowing businesses to meet high production demands without delays.
For instance, a fully automated machine can wrap up to 60 coils per hour, compared to the 10–15 coils typically wrapped manually. This sixfold increase in productivity enables manufacturers to handle larger orders and meet tighter deadlines without hiring additional labor. Furthermore, automation eliminates errors such as loose or uneven wrapping, ensuring every product is packaged securely and consistently.
1.4 Benefits of Faster Wrapping Cycles for Workflow Optimization
Faster wrapping cycles directly impact workflow efficiency by reducing bottlenecks and enabling seamless transitions between production and packaging. Key benefits include:
- Improved Throughput: Automated machines keep pace with production lines, ensuring no backlogs in packaging.
- Reduced Labor Costs: One operator can oversee multiple machines, minimizing workforce requirements.
- Consistent Output: Every package meets the same high-quality standards, reducing rework and returns.
- Enhanced Scheduling: Faster wrapping allows for more accurate delivery timelines, improving customer satisfaction.
For example, a manufacturer wrapping 200 coils daily with a manual process might spend 20 labor hours on packaging. By switching to automation, this task could be completed in just 4–5 hours, freeing up resources for other critical operations.
1.5 Fact Check: Does Automation Always Improve Workflow?
- True: Automation significantly improves workflow by increasing speed, reducing errors, and minimizing labor dependency, especially in high-volume operations.
- False: Automation is a guaranteed solution for all businesses. For low-volume operations, the cost of automation may outweigh its benefits, making manual or semi-automatic systems more practical.
2. What Specific Features of Automated Coil Wrapping Machines Improve Workflow?
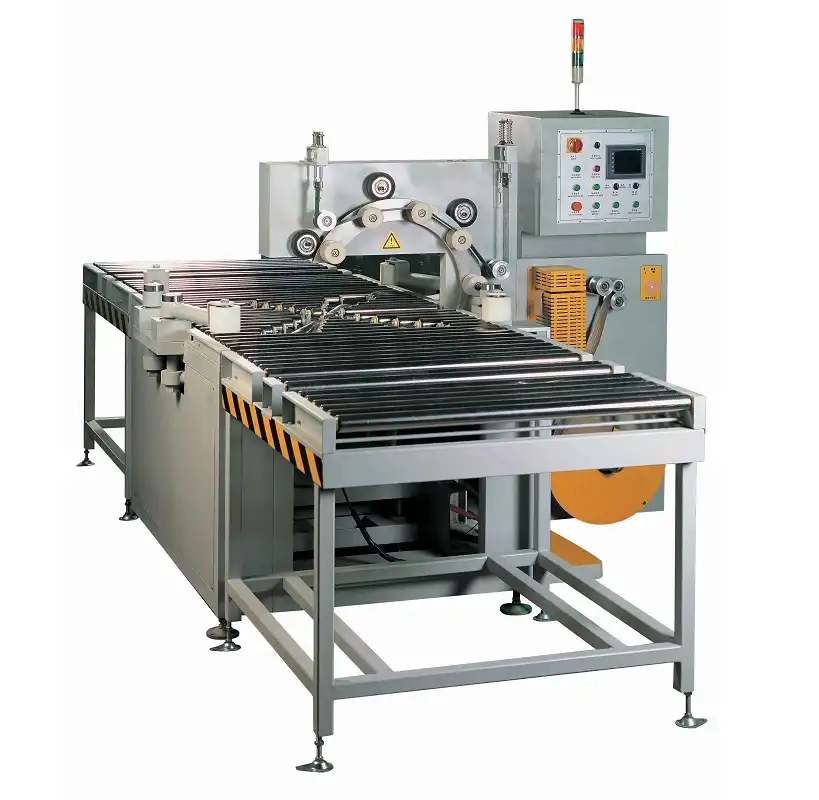
2.1 Key Features That Save Time and Effort
Automated coil wrapping machines are designed with features that significantly enhance operational efficiency. These features not only reduce time spent on packaging but also ensure consistent quality and minimal material waste.
Some of the most impactful features include:
- Automatic Film Tensioning: Ensures the wrapping material is applied evenly, reducing human error and minimizing product damage.
- Pre-Stretch Technology: Allows the machine to stretch the film before application, reducing material usage by up to 30%.
- Programmable Logic Controller (PLC): Provides precision and flexibility by enabling operators to set specific wrapping parameters for different coil sizes and shapes.
- Integrated Loading Systems: Automates the loading and positioning of heavy steel coils, reducing operator effort and speeding up the process.
- High-Speed Rotation Systems: Increases wrapping speed while maintaining consistent tension and coverage.
These features work together to optimize the entire wrapping process, allowing businesses to package more products in less time while maintaining high-quality standards.
2.2 Feature Comparison Between Manual, Semi-Automatic, and Automatic Machines (With Table)
Understanding how different types of machines compare in terms of features can help you decide which one is best suited for your operations:
Feature | Manual Wrapping | Semi-Automatic Machines | Automatic Machines |
---|---|---|---|
Speed | 5–10 coils/hour | 15–30 coils/hour | 30–60 coils/hour |
Operator Involvement | High | Moderate | Minimal |
Film Tension Control | None | Partial | Full |
Material Usage | High (Wasteful) | Moderate | Low (Optimized) |
Customization | Limited | Moderate | High |
Automation Level | None | Partial | Full |
As shown in the table, fully automated machines offer superior speed, precision, and material efficiency, making them ideal for high-volume operations. Semi-automatic machines, on the other hand, strike a balance between cost and performance, while manual wrapping is best suited for low-volume, budget-conscious businesses.
2.3 Advanced Features That Address Industry-Specific Needs
Certain industries require specialized packaging solutions that go beyond standard features. Automated coil wrapping machines are now equipped with advanced functionalities to meet these unique demands:
- Multi-Layer Wrapping: Provides additional protection for products exposed to harsh environmental conditions, such as moisture or corrosion.
- Edge Protection Systems: Applies protective materials to the edges of steel coils to prevent damage during transportation.
- Dual Film Roll Systems: Enables the machine to apply two layers of film simultaneously for added durability.
- IoT Integration: Allows operators to monitor machine performance and production metrics remotely, ensuring uninterrupted operations.
For instance, a steel manufacturer operating in coastal regions might prioritize machines with multi-layer wrapping and edge protection systems to safeguard their products against humidity and salt exposure.
2.4 Conclusion
Automated coil wrapping machines stand out due to their time-saving features, precision, and ability to meet specialized packaging needs. For businesses aiming to optimize workflow, these machines offer unmatched efficiency and flexibility. By leveraging advanced features such as PLCs, pre-stretch technology, and IoT integration, manufacturers can streamline their operations, reduce material waste, and achieve consistent packaging quality.
Whether you’re handling standard coils or require specialized wrapping solutions, investing in the right machine features can transform your packaging process and eliminate bottlenecks.
2.5 Fact Check: Are Advanced Features Always Necessary?
- True: Advanced features like IoT integration and multi-layer wrapping are crucial for businesses with industry-specific requirements or high production volumes.
- False: Every business needs advanced features. For smaller operations, simpler machines with basic automation may suffice, offering a more cost-effective solution.
3. How Do Automated Machines Reduce Operational Delays?

3.1 Common Causes of Delays in Manual Wrapping (With Table)
Manual wrapping processes are often plagued with inefficiencies that lead to significant operational delays. Here are the most common causes of delays and how automation addresses them:
Cause of Delay | Manual Wrapping | Automated Machines |
---|---|---|
Slow Wrapping Speed | Limited by human effort | High-speed rotation systems |
Inconsistent Tension | Results in rework or damage | Uniform and precise tension |
Frequent Breaks | Operators require rest | Continuous operation |
Material Waste | Requires frequent refills | Optimized usage, fewer refills |
Heavy Coil Handling | Time-consuming and labor-intensive | Automated loading systems reduce effort |
This comparison illustrates how automation eliminates bottlenecks, enabling businesses to improve throughput and meet tight deadlines.
3.2 Streamlining Packaging with Automation for Maximum Efficiency
Automated machines streamline the packaging process in several ways:
- Continuous Operation: Unlike manual processes that are interrupted by operator fatigue or breaks, automated machines can run continuously, ensuring uninterrupted workflow.
- Rapid Setup and Changeover: Many automated machines allow operators to switch between coil sizes and wrapping patterns with minimal downtime, increasing overall efficiency.
- Error Reduction: Machines equipped with sensors and programmable controllers ensure precise wrapping, reducing the need for rework.
For example, a manufacturer using a manual process to wrap 100 coils per day might spend 10–12 labor hours on packaging. With an automated machine, the same task could be completed in 2–3 hours, significantly boosting productivity.
3.3 Exploring How Automated Machines Improve Supply Chain Speed
Efficient packaging plays a crucial role in maintaining supply chain speed. Automated machines contribute to faster operations in the following ways:
- Shorter Lead Times: By reducing packaging time, businesses can fulfill orders more quickly.
- Reduced Downtime: Machines with advanced diagnostics and IoT capabilities can detect potential issues early, preventing unexpected breakdowns.
- Improved Logistics: Consistently wrapped coils are easier to stack, store, and transport, streamlining the logistics process.
For instance, a business operating in the steel industry might see a 25% reduction in delivery time by automating its packaging process, enabling it to meet customer demands faster and more reliably.
3.4 Dive Deeper into Maintenance and Downtime Reduction
While automated machines are designed for efficiency, regular maintenance is essential to avoid unexpected downtime. Here’s a breakdown of maintenance tasks and their impact:
Task | Frequency | Impact |
---|---|---|
Lubricating Components | Weekly | Prevents wear and tear, ensuring smooth operation |
Inspecting Sensors | Monthly | Ensures accurate tension and wrapping patterns |
Cleaning the Machine | Daily | Prevents debris buildup that could affect performance |
Replacing Worn Parts | As Needed | Reduces the risk of breakdowns |
Machines with built-in diagnostic systems can alert operators of maintenance needs, reducing unplanned downtime and ensuring continuous operation.
3.5 Fact Check: Do Automated Machines Eliminate Delays Entirely?
- True: Automated machines drastically reduce delays by optimizing speed, accuracy, and material usage in the packaging process.
- False: Automated machines eliminate all delays. Factors such as maintenance requirements, operator training, and unexpected technical issues can still cause occasional disruptions.
4. What Are the Long-Term Benefits of Automation in Coil Wrapping?

4.1 Cost Savings Through Reduced Labor and Material Waste
One of the most significant long-term benefits of automated coil wrapping machines is cost savings. While the initial investment in automation might seem substantial, the reduction in labor costs and material waste quickly offsets this expense.
Automated machines reduce dependency on manual labor, allowing businesses to reallocate workers to higher-value tasks. For example, instead of employing five workers to manually wrap coils, a single operator can manage the entire process with an automated machine. This shift not only reduces payroll costs but also improves overall productivity.
Material efficiency is another key factor. Automated machines use advanced film tension control and pre-stretch technology to optimize material usage. This ensures that the exact amount of wrapping material is applied, minimizing waste and reducing packaging expenses by up to 30%.
Over time, these cost savings compound, making automation a highly profitable investment for medium- to large-scale businesses.
4.2 ROI Analysis of Automated Coil Wrapping Machines (With Table)
Calculating the return on investment (ROI) for an automated coil wrapping machine can help businesses understand the financial advantages of automation. Here’s an example of a cost-benefit breakdown:
Factor | Manual Wrapping | Automated Wrapping | Savings |
---|---|---|---|
Labor Cost (Yearly) | $50,000 (5 workers) | $10,000 (1 operator) | $40,000 |
Material Waste | 20–30% | 5% | 15–25% |
Maintenance Cost | Minimal | Moderate | - |
Production Speed | 10–15 coils/hour | 40–60 coils/hour | 3–4x faster |
In this example, the automated machine costs $30,000 upfront but saves $40,000 annually in labor costs alone. This means the payback period is less than one year, after which the business continues to benefit from increased efficiency and reduced expenses.
4.3 Long-Term Scalability with Automated Systems
As businesses grow, their packaging needs often outpace the capabilities of manual or semi-automatic processes. Automated coil wrapping machines are designed with scalability in mind, making them a future-proof solution for growing operations.
- Increased Production Capacity: Automated machines can handle higher volumes without additional labor costs, allowing businesses to scale up operations seamlessly.
- Customizable Features: Many machines are equipped with adjustable settings and modular components, enabling them to adapt to changing product dimensions and packaging requirements.
- Integration with Production Lines: Advanced machines can be integrated into existing production lines, creating a fully automated workflow that eliminates bottlenecks.
For example, a steel manufacturer producing 200 coils per day may initially invest in a semi-automatic machine but later upgrade to a fully automatic system as production volumes increase. This scalability ensures that the packaging process keeps pace with growth, eliminating the need for costly overhauls or manual labor expansion.
4.4 Dive Deeper into Sustainability Benefits of Automation
Beyond cost savings and efficiency, automated coil wrapping machines offer significant sustainability benefits. These include:
- Reduced Material Waste: By optimizing film usage, automated machines lower the amount of plastic waste generated, contributing to a more sustainable packaging process.
- Energy Efficiency: Many modern machines are designed to consume less energy, reducing the carbon footprint of operations.
- Support for Eco-Friendly Materials: Advances in wrapping technology now allow machines to work with biodegradable or recyclable films, helping businesses meet environmental regulations and consumer expectations.
For instance, a business that reduces its material waste by 25% through automation could save thousands of dollars annually while also meeting corporate sustainability goals. These eco-friendly improvements can enhance brand reputation and appeal to environmentally conscious customers.
Fact Check: Automation’s Long-Term Benefits
- True: Automated coil wrapping machines offer substantial long-term benefits, including cost savings, scalability, and sustainability, making them a valuable investment for growing businesses.
- False: Automation eliminates the need for maintenance and operator involvement. While machines reduce manual labor, they still require regular upkeep and trained operators to ensure optimal performance.
Conclusion

[claim] Automated coil wrapping machines represent a transformative solution for businesses seeking to optimize workflow, reduce operational delays, and future-proof their packaging processes.
By replacing manual methods with automation, businesses can achieve faster production speeds, consistent packaging quality, and significant cost savings. Automated machines minimize labor dependency, reduce material waste, and eliminate common bottlenecks, enabling manufacturers to scale operations effortlessly and meet growing demand.
The benefits of automation extend beyond efficiency. With advanced features like pre-stretch technology, IoT integration, and compatibility with sustainable materials, these machines offer long-term advantages that align with modern business needs. Whether it’s improving supply chain speed, reducing carbon footprints, or enhancing customer satisfaction, automated wrapping machines deliver value on multiple fronts.
For businesses hesitant to make the leap, ROI analysis shows that the initial investment in automation can be recouped within months, followed by years of increased productivity and reduced costs. Transitioning to automation is not just a step forward—it’s a strategic move that ensures competitiveness and growth in an ever-evolving market.
In conclusion, investing in an automated coil wrapping machine is more than just upgrading your packaging process; it’s about transforming your business’s efficiency, sustainability, and scalability for the future.